Falls ihr dann wirklich irgendwann an dem Punkt seid, dass ihr glaubt euer Uboot wäre fertig, ist es das beste einen Pool zu bauen damit nicht gleich alle lachen, wenn das Ding im See untergeht und nicht wieder auftaucht.
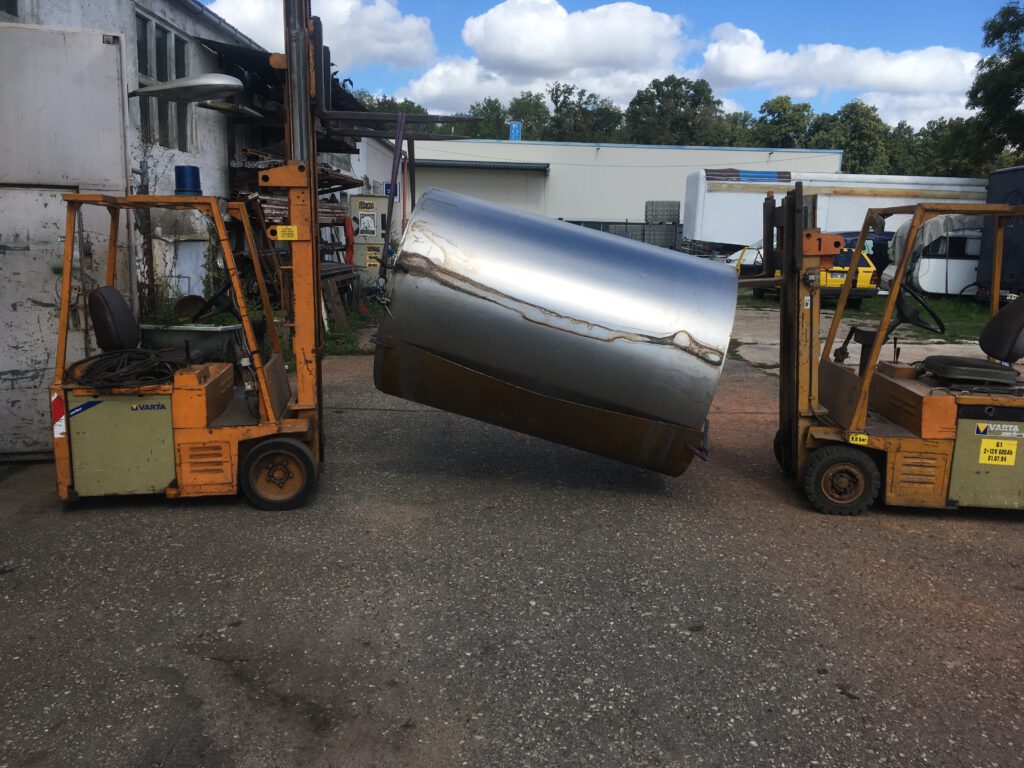
Dazu braucht es erstmal einfach eine Rolle Stahl.
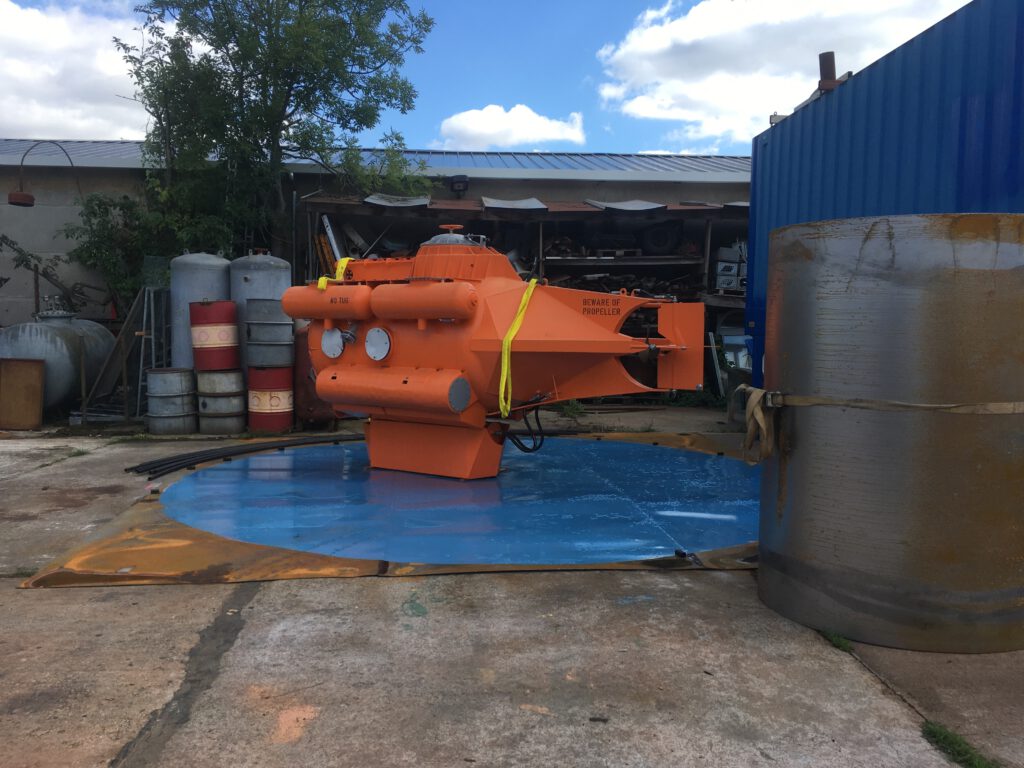
Wenn man sich den Kran zum Uboot reinheben sparen will, sollte man am besten den Pool um das Uboot drumherum bauen.
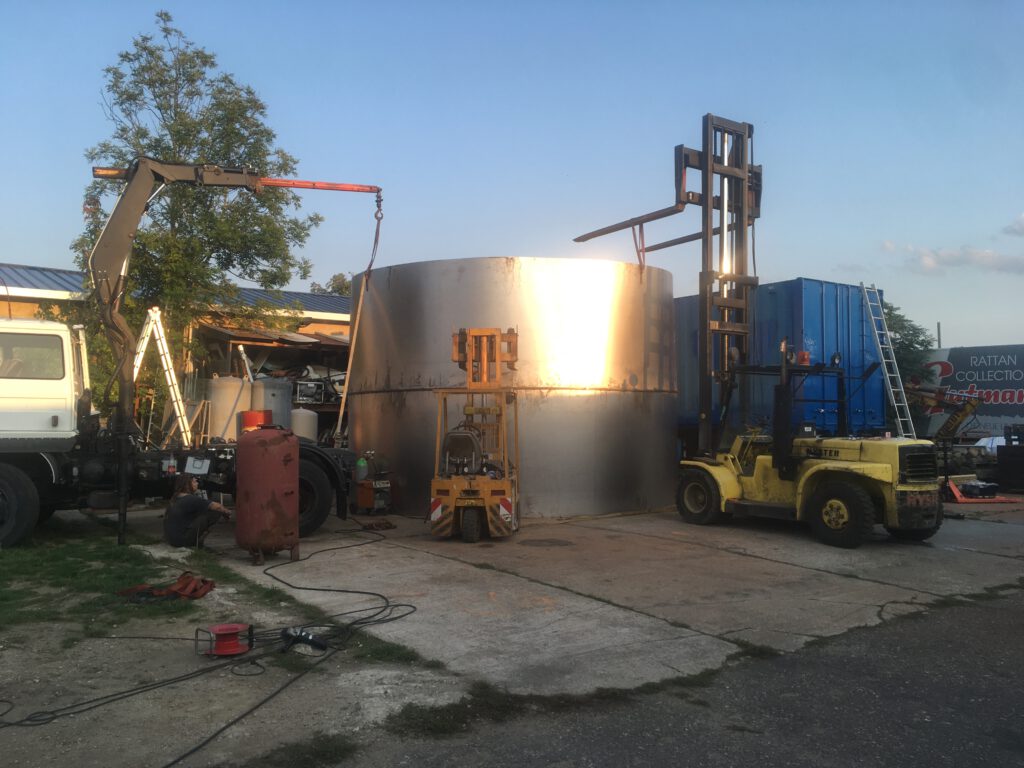
Am besten fragt man die Nachbarn an ob sie nicht an einer Baumaschinenausstellung auf dem Hof teilnehmen möchten. So gibt es genügend Geräte den oberen Ring aus Blech auf den Unteren zu heben.
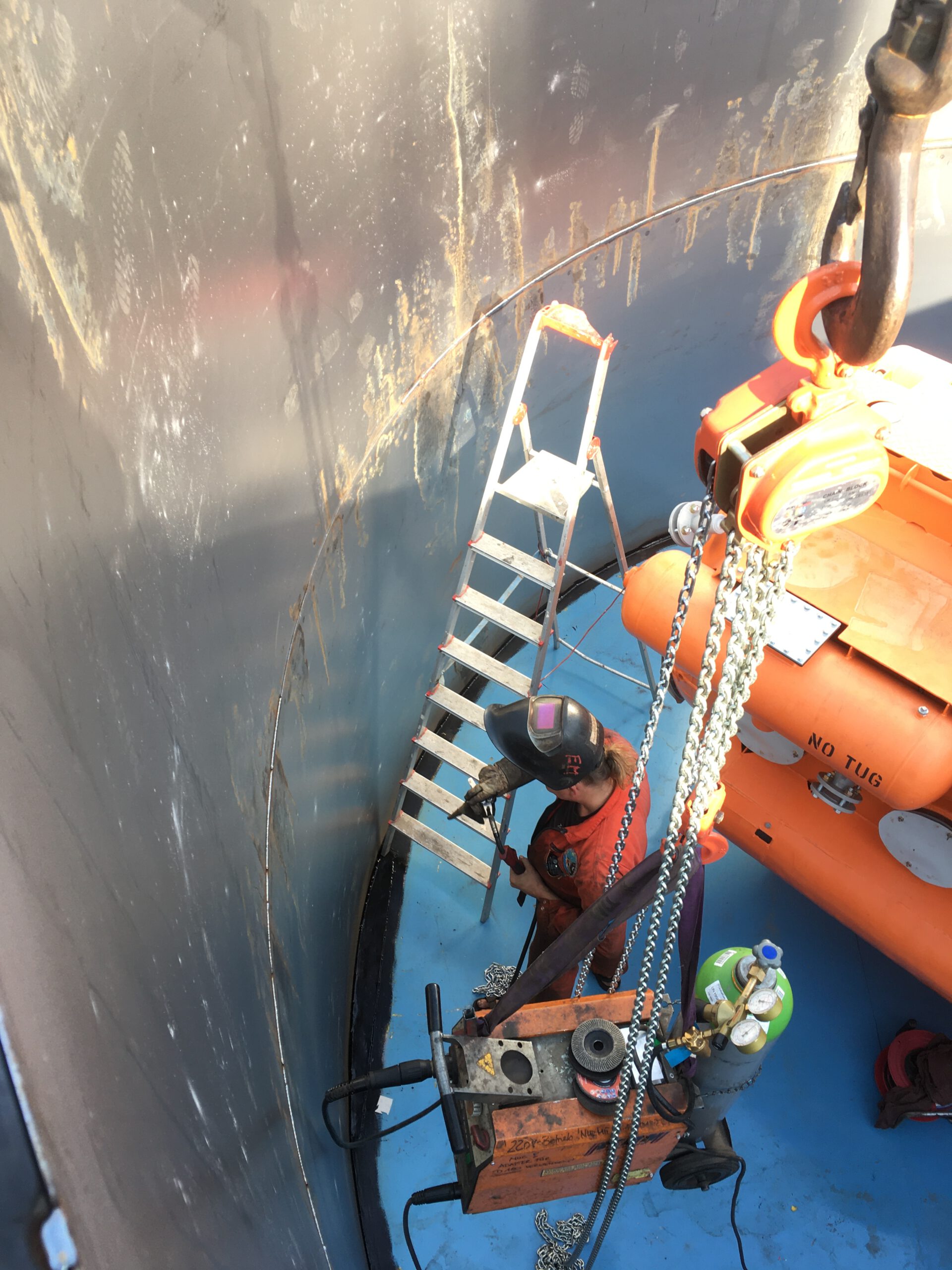
Cirka 60 Meter wasserdichte Schweißnaht später ist es Zeit über Farbe nachzudenken.
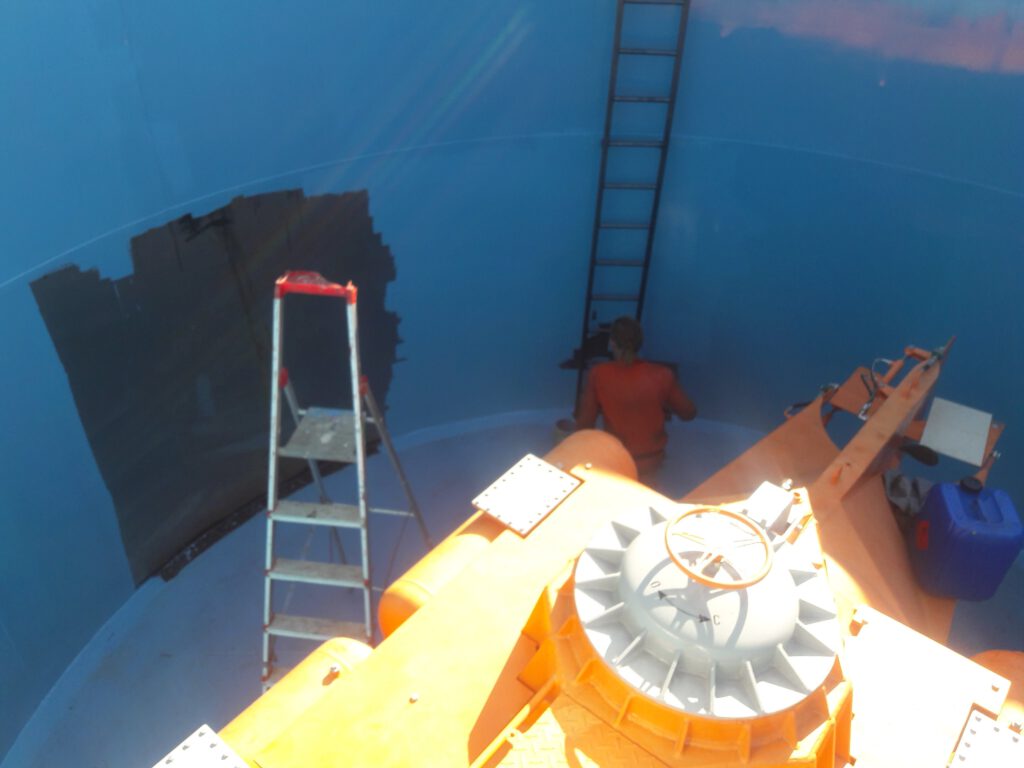
Hier wurden verschiedene verbeulte Restdosen in allerlei Farbtönen aus einem Unfallschaden diletantisch zu einem Poolblau zusammen gemischt.
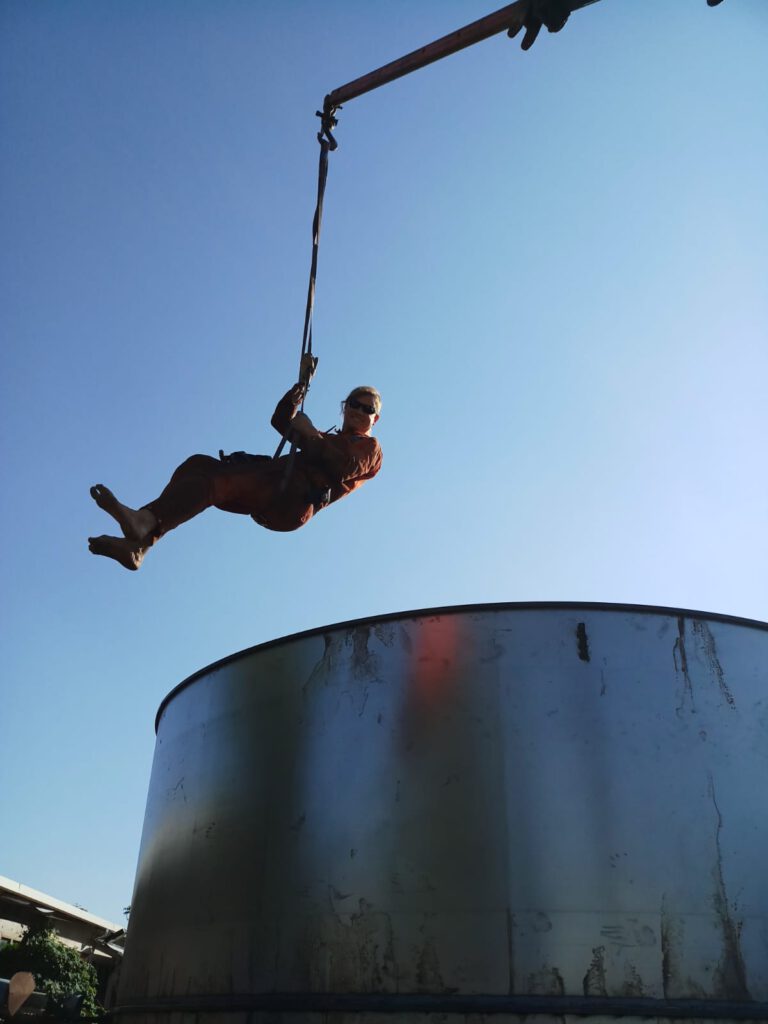
Frisch gestrichene Pools werden am besten durch die Luft verlassen.
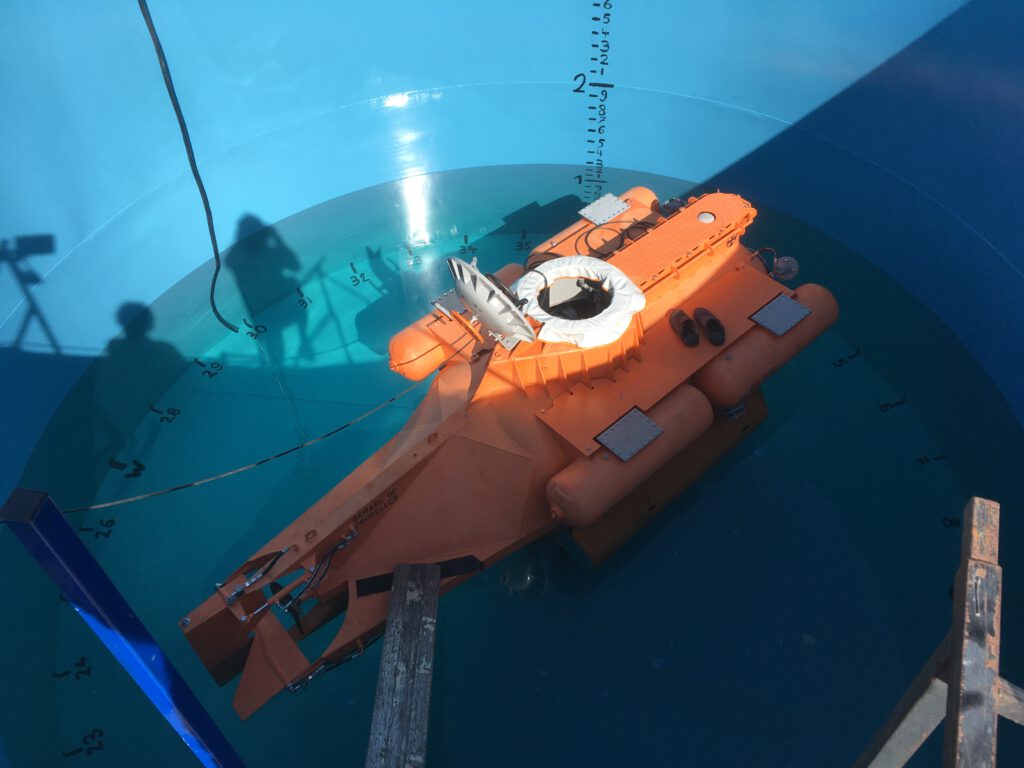
Dann bleibt nur noch den Wasserhahn aufzudrehen und zu hoffen, dass alles dicht ist.